7 Ways eLearning Can Drive Efficiency in the Manufacturing Sector
Want to boost training efficiencies in the manufacturing sector? eLearning is your best bet to do so, read on to explore how...
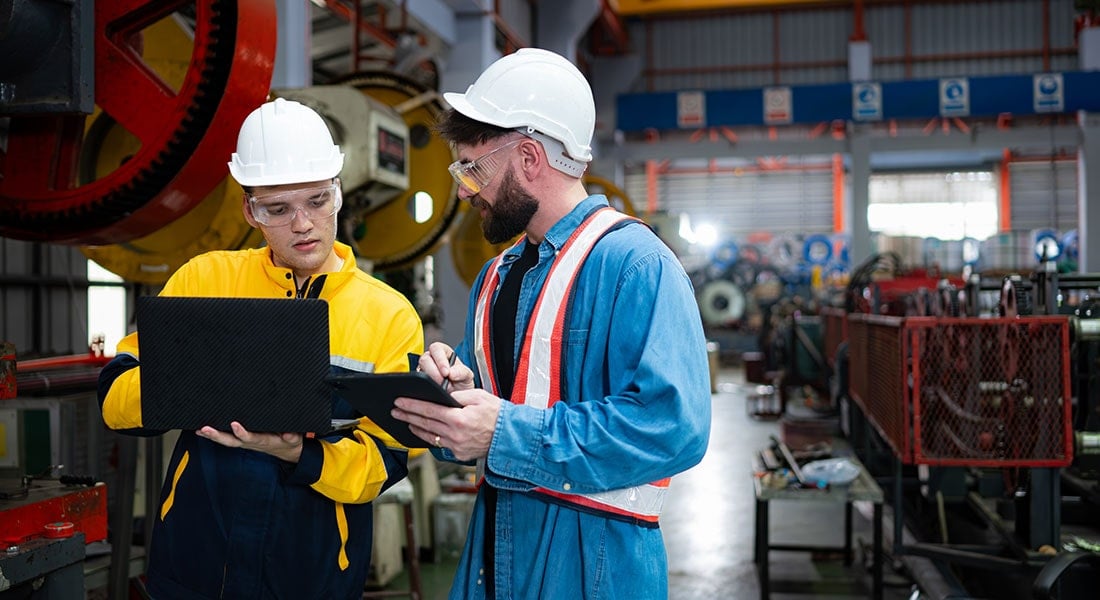
The manufacturing industry thrives on precision and efficiency. Every person associated with the machine, from the assembly line worker to the quality control specialist, plays a crucial role in ensuring smooth operations and high-quality output. But with the ever-evolving landscape of technology and best practices, traditional training methods can struggle to keep pace. Enter eLearning for the manufacturing industry, a powerful tool that can revolutionize how you train your workforce and drive efficiency across the board.
How Can eLearning Drive Efficiencies in the Manufacturing Sector?
- Microlearning: Short, impactful modules for busy schedules.
- Video-Based Learning: Engaging visuals bring concepts to life.
- Custom eLearning: Tailored training for specific needs.
- Gamification: Makes learning fun and fosters competition.
(Read on to explore more)
Let us discuss how eLearning transforms manufacturing training and unlock a new era of operational excellence:
7 Ways eLearning Can Drive Efficiency in the Manufacturing Industry
1. Microlearning for Maximum Impact
In today's busy work environments, long training sessions can be disruptive and lead to information overload. Microlearning offers a refreshing alternative. Bite-sized learning modules, delivered in short bursts (think 5-10 minutes), allow employees to learn new skills or refresh existing knowledge on their own time, at their own pace. This targeted approach improves knowledge retention and reduces overall training time, leading to increased productivity on the job.
Imagine: Short, engaging video tutorials on specific procedures for operating new machinery. These microlearning modules can be easily accessed on tablets or smartphones directly on the factory floor, minimizing disruption and maximizing knowledge transfer.
2. Video-Based Learning: Bringing Concepts to Life
Manufacturing processes can be complex and visually intricate. Traditional text-based training materials may not always do justice to the skillsets required. Video-based learning comes to the rescue! Videos can demonstrate procedures, showcase real-world scenarios, and even utilize 3D animations to explain complex technical concepts. This visually immersive format fosters deeper understanding and engagement, leading to fewer training errors and improved job performance.
For example: Develop a video series demonstrating proper maintenance procedures for critical equipment. These videos, translated into multiple languages for a global workforce, can ensure consistent understanding and application of best practices across all teams.
How to Plan and Design Video-Based Learning [Video]
3. Custom eLearning: Tailored Training for Specific Needs
A one-size-fits-all training approach simply doesn't cut it in the diverse world of manufacturing. Custom eLearning allows you to create targeted training programs that address the specific needs of each department, role, or even individual skill gaps. This customization ensures that employees receive relevant and applicable training, leading to improved performance and a more efficient overall training process.
Consider: Develop custom eLearning modules for onboarding new employees, tailored to their specific roles within the manufacturing process. This targeted approach reduces overall training time and ensures new hires are quickly equipped with the knowledge and skills needed to contribute effectively.
Here's an insightful infographic to help you explore more about custom eLearning: Custom eLearning 101
4. Gamification: Make Learning Fun and Engaging!
Manufacturing training doesn't have to be dry and monotonous. Gamification introduces elements of game design – points, badges, leaderboards – into the eLearning experience. This playful approach promotes healthy competition, motivates learners to complete modules, and fosters a more engaging learning environment.
In action: Develop a gamified eLearning program for safety protocols. Learners can navigate interactive scenarios, earn points for following safe practices, and even compete with colleagues on a virtual leaderboard. This engaging format reinforces safety awareness in a fun and memorable way.
→ Download Now: How to select the Right eLearning Vendor? [eBook]
5. Translation and Localization for a Global Workforce
The manufacturing industry operates on a global scale. To ensure seamless communication and efficient operations, it's crucial to provide training materials in the native languages of your workforce. Translation and localization services for eLearning modules can break down language barriers and empower employees from diverse backgrounds to fully grasp training content.
The benefit: Develop a core eLearning module on lean manufacturing principles and translate it into multiple languages for your international facilities. This ensures consistent understanding of these crucial efficiency practices across your global operations.
6. Blended Learning: The Best of Both Worlds
While eLearning offers numerous advantages, there's still a place for traditional instructor-led training. Blended learning combines eLearning modules with hands-on workshops, group discussions, and facilitated learning activities. This approach leverages the strengths of both methods – the self-paced flexibility of eLearning with the interactive benefits of face-to-face instruction – to create a well-rounded learning experience that caters to diverse learning styles and maximizes knowledge retention.
The strategy: Use eLearning modules to introduce basic concepts and procedures related to machine operation. Then, conduct hands-on workshops facilitated by experienced trainers. This blended approach allows employees to grasp theoretical knowledge through eLearning and then solidify it through practical application in a workshop setting.
7. The Power of Outsourcing: Accessing Expertise and Scalability
Developing and maintaining a robust eLearning program for the manufacturing industry can require specialized skills and ongoing resources. Outsourcing eLearning development to a professional Learning and Development (L&D) company allows you to leverage their expertise in instructional design, multimedia development, and learning management systems. This not only saves you time and resources but also ensures access to the latest eLearning technologies and methodologies.
The solution: Partner with an L&D company to develop a comprehensive eLearning program for quality control procedures. Their expertise can ensure clear, concise training modules that are aligned with your quality standards and regulatory requirements.
Conclusion: The eLearning Revolution in Manufacturing
By embracing eLearning, manufacturing companies can unlock a new era of efficiency and productivity. From bite-sized microlearning modules to engaging gamified experiences, eLearning offers a plethora of tools to empower your workforce and optimize your training processes. Remember, a well-designed eLearning strategy is not just about acquiring new skills; it's about creating a culture of continuous learning and improvement within your organization.
Ready to embark on your eLearning journey? Looking for an eLearning outsourcing partner? Here's a resource to help you find the right partner: